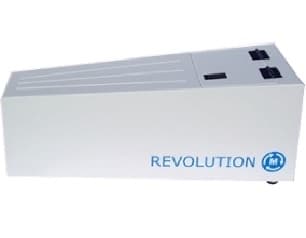
Revolution – Caking Application Note
The effects of caking on the dynamic flow of cohesive powders
Abstract
Caking or the bonding of particles due to inter-particle cohesion has a huge effect on the behaviour of powders. Strong bonds between particles can prevent materials from exiting silos and storage containers. However, under dynamic conditions, caking can actually improve the flow properties of the material. Caking in powders occurs in two ways. Under static conditions as in storage containers and silos, caking occurs due to particles being pressed together by the force of gravity acting on a column of material or by external forces. Generally the stronger the forces acting on the material the stronger the bonds between cohesive particles. Under dynamic conditions, caking occurs due to particles smashing together as they flow. This type of caking is also referred to as agglomeration, clumping or granulation. Dynamic conditions are defined as situations where a powder is moving under the influence of gravity or by mechanical convection. In industry, powders are typically stored under static conditions but are used under dynamic conditions. Therefore, the characteristics of the material after storage under static conditions as well as the stability of the material under dynamic conditions are critical to the successful use of the material. In this study, the effects of caking under static and dynamic conditions on the dynamic flow characteristics of powders are analysed. Powders with different degrees of inter-particle cohesion are studied using uni-axial compression to simulate static conditions and a rotating drum to simulate dynamic conditions. The assessment of the inter-particle cohesion of the material is achieved by measuring the unconfined yield strength of the material after a consolidating stress has been applied. It is found that caking due to inter-particle cohesion under both static and dynamic conditions directly affects the dynamic flow characteristics of powders and also can create instabilities in these characteristics as the materials are subjected to dynamic forces. The dynamic flow characteristics measured include avalanche energy and dynamic density. It is also found that the level of caking in a powder can be assessed by measuring the changes in its dynamic flow characteristics before and after exposure to static and dynamic conditions.
IntroductionCohesive powders are widely used in industry. The ability to understand and predict the behaviour of these powders is critical to their successful manufacture, storage, and use. Yet cohesive powders are very unpredictable due to their changing nature. The main problem with cohesive powders is the ability of the powder particles to bond in a process typically referred to as caking. Particles of the powders come in contact and bond together to form larger particles, clusters of particles or clumps of particles. There are several mechanisms for this caking (Röck 2005) but generally it occurs in two ways. Under static conditions, as in storage containers and silos, caking occurs due to particles being pressed together by the force of gravity acting on a column of material or by external forces. Generally the stronger the forces acting on the material the stronger the bonds between cohesive particles. Under dynamic conditions, caking occurs due to particles smashing together as they flow. This type of caking is also referred to as agglomeration, clumping or granulation.
Much work has been done to understand the effects of caking on the flow of cohesive powders from storage containers, silos, and large industrial totes (Jenike,1961). Most of this work is focused on whether or not the powder will flow from the storage system. But once out of the storage system, how will the powder perform? Has its behaviour been altered by the presence of agglomerated particles and clumps after storage? These questions are very important as powders are typically used under dynamic conditions.
Dynamic conditions are defined as situations where a powder is moving under the influence of gravity or by mechanical convection. These conditions are present in pneumatic conveyors, tableting machines, powder spraying systems, mixing systems, etc. In industry, powders are typically stored under static conditions but are used under dynamic conditions. Therefore, the characteristics of the material after storage under static conditions as well as the stability of the material under dynamic conditions are critical to the successful use of the material. Many powder application problems in industry are caused by cohesive powders changing their behaviour after storage.
In this study, the effects of caking under static and dynamic conditions on the dynamic flow characteristics of powders are analysed. Powders with different degrees of inter-particle cohesion are studied using uni-axial compression to simulate static conditions and a rotating drum to simulate dynamic conditions. The assessment of the inter-particle cohesion level of the material is achieved by measuring the unconfined yield strength of the material after a consolidating stress has been applied.
MaterialsA range of commercially available materials were chosen for this study to reflect powders with different levels of cohesion, including carbon black, limestone, copper sulphate, micro-crystalline cellulose, and powdered sugar. Three sets of these samples with the same specifications had performance differences in industrial applications: 1) carbon black-1 agglomerated less than carbon black-2, limestone-2 pneumatically conveyed better than limestone-1, and the copper sulphate samples flowed differently in the application. Samples were de-agglomerated to remove clumps and aggregates and stabilised to ambient conditions for one day.
EquipmentThe Evolution Powder Tester (EPT) from Mercury Scientific Inc. was used to assess the cohesion level of the samples. The Evolution measures the unconfined yield strength of materials at pressures up to 500 kPa by compressing and breaking powder samples. The first step of the test is compressing the sample in an analysis cell by vertical pressure. The vertical pressure is applied by the instrument for short periods or by weights for longer periods to simulate storage conditions. After compression, the sample is then automatically removed from the sample cell and force is applied to the top of the sample to cause the material to yield. The maximum force recorded when the sample yields is the unconfined yield strength. The stress applied to the sample is the major consolidation stress.
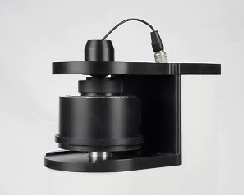
Figure 1: Sample being compressed on the Evolution Powder Tester
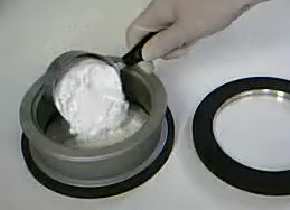
Figure 2: Filling the Revolution Powder Analyser sample drum
The Revolution Powder Analyser (RPA) from Mercury Scientific Inc. was used to assess the dynamic flow behaviour of the samples and to simulate dynamic process conditions. The Revolution Powder Analyser consists of a rotating drum that measures the flow properties of granular and fluidised materials. A stepper motor turns high precision silicone rollers which in turn rotates the drum. The drum rotation rate can range from 0.1 to 200 RPM. A digital camera with the assistance of back-light illumination takes digital images of the powder during the rotation process. The instrument’s software measures the behaviour of the powder from the images collected due to the drum rotation and how this behaviour changes over time. This data is then used to calculate various parameters representing the powder’s quality and flow characteristics.
ExperimentalThe unconfined yield strength of the samples were measured to quantify their cohesion levels. The pressure level chosen for the analysis was 15 kPa, representing a a stress level in industrial storage containers. 80 cc’s of each powder sample were loaded into the test cells of the Evolution Powder Tester following the manufacturer’s recommend procedure and were compressed by 15 kPa of pressure for 60 seconds. After compression, the instrument removed the consolidated samples from the test cells and the force required to make the samples yield was measured. This force is the unconfined yield strength.
The initial dynamic flow properties of the samples were then measured using the flowability test of the Revolution Powder Analyser. 100 cc’s of each powder sample were loaded into the instrument’s sample drum and the drum rotation was started at 0.3 RPM (revolutions per minute). After a conditioning time of 90 seconds, the instrument measured the avalanche energy and dynamic density of the samples. The avalanche energy is the change in potential energy before and after an avalanche as sample is rotated in the sample drum. The reported value is an average of 100 avalanches normalised by the sample weight. The lower the avalanche energy, the better the material flows. The dynamic density is the density of the sample as measured in the sample drum during the drum rotation.
To expose the sample to agglomerating forces, the sample drum speed was then increased to 20 RPM for a period of 20 minutes. This rotational movement produced low velocity collisions between the sample particles. These collisions can have enough force to cause sample particles to stick together and form large clumps of caked or agglomerated particles. The flowability test was then run again to measure the changes in the sample.
After the agglomeration procedure, each sample was removed from the sample test drum, deagglomerated and loaded into a compression cup to simulate storage conditions. A lid was placed on the sample and a consolidation force of 15 kPa was applied to the samples by weights for 30 minutes. The sample was then transferred from the compression cup back to the sample drum of the Revolution Powder Analyser and the dynamic flow properties of the samples where measured again.
Results and DiscussionsResults for the unconfined yield strength and dynamic flow tests are presented in Table 1. Samples are listed in the order corresponding to their unconfined yield strength.
All of the tested samples had unconfined yield strengths that rank the sample materials as cohesive according to accepted classifications (Fitzpatrick,2004). The flow factors for these samples (the major consolidation stress / the unconfined yield strength) are from 2 to 4. The dynamic flow of the samples ranged from easy flowing (avalanche energy < 20 kJ/kg) to poor flowing (avalanche energy > 50 kJ/kg).
The results between the unconfined yield strength tests and the dynamic flow tests indicate that unconfined yield strength is not a strong predictor of a material’s dynamic flow properties. This is clear in comparing the ranking of materials by unconfined yield strength and avalanche energy. The carbon black samples had higher unconfined yield strengths but had the lowest avalanche energies while the micro-crystalline cellulose had the lowest unconfined yield strength but mid-level avalanche energy.
In comparing the dynamic flow behaviour before and after the samples were exposed to caking or consolidating pressure, the dynamic density increased for all of the samples tested and the dynamic flowability improved for all but one sample. This is as expected. These changes are due to the formation of clumps of particles in the samples that remained after the initiation of flow. This indicates that powders with cohesion that are exposed to consolidating pressure will flow differently in dynamic conditions after the pressure has been removed unless enough energy is applied to the sample to break the caked particles apart. The forces acting on the sample in the Revolution sample drum are very low, being generated only by the weight of the material itself. The strength of these forces can be estimated by dividing the maximum energy of the sample before an avalanche by the area of the sample. This calculation gives a pressure range of 50 to 150 Pascals for the tested samples. These forces are in the same range as forces acting on materials in feeders, filling machines, and tablet presses and are typically large enough to break most of the clumps of particles in the samples even though the total strength of the caked sample is much higher.
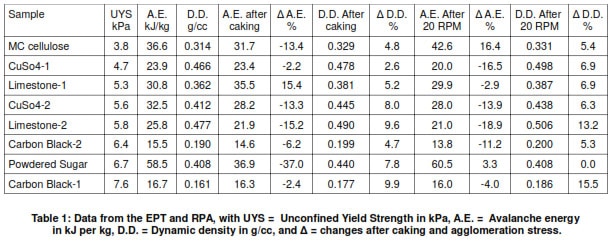
The dynamic flow results also did not trend well with the unconfined yield strength results but the dynamic density results where more in line with the strength data. From visually inspecting the samples, this indicates that the avalanche energy is more affected by the size of the clumps of particles left in the samples rather than their strength while the dynamic density is more affected by the strength of the bonds between the particles. This is illustrated by comparing the data for the powdered sugar and carbon black-1 samples. The powdered sugar formed large clumps which had a large effect on the dynamic flow of the sample, changing its avalanche energy 38%. But the dynamic density of the sugar only changed 7.8%. The carbon black-1 sample showed only a 2.4% change in its avalanche energy but a 9.9% change in its dynamic density. The carbon black sample visually formed only very small clumps and this is represented by a small change in the avalanche energy.
In comparing the dynamic flow behaviour before and after the samples were exposed to agglomerating stress, the dynamic density increased and the dynamic flowability improved for most of the samples. This data indicates that caking or clumping of particles occurs under dynamic conditions. This is well known and expected as many materials are intentionally agglomerated under dynamic conditions in fluid bed or rotating drum agglomeration. However, this suggests that handling alone can cause unintended and unwanted agglomeration in cohesive powders that affect their behaviour.
The agglomeration data does not trend with the unconfined yield strength data. The powdered sugar sample had a high strength but showed almost no change in its avalanche energy or dynamic density after being exposed to agglomeration stress. This is most likely due to the large differences in the scale of the forces acting on the sugar in the unconfined yield strength test versus the agglomeration test. As per above, the forces acting on the samples in the Revolution sample drum are low. It could be that for some materials these forces are not large enough to cause bonding between adjacent particles as in the unconfined yield strength test where the forces are high enough to cause particles to stick together. The limestone-2 sample had large changes in its avalanche energy and dynamic density but had a middle unconfined yield strength. This could be a result of more efficient bonding of particles due to more particle to particle interactions than in a static consolidating condition. In either case and in general, the unconfined yield strength was not a reliable predictor of agglomeration behaviour.
In comparing the caking data to the agglomeration data, agglomeration due to particle motion had more effect on dynamic flowability and density than caking due to consolidating pressure. Of the samples that both caked and agglomerated, the agglomerated samples had a higher dynamic density than the caked samples and they had lower avalanche energies. The avalanche energy results may be a result of the agglomerated particles being very round when formed by dynamic motion. For caked samples, the shapes of the agglomerated particles are random and highly shaped. This may also explain the density effects as the round particles pack more efficiently in the powder bed. Regardless of the cause, the end results is that handling powder may be more of an issue in changing the flow behaviour of powders than consolidating pressure.
In reviewing all of the test data, it is clear that the caking or aggregation level of the particles in a powder sample have a large effect on its dynamic flow behavior, specifically its avalanche energy and dynamic density. Therefore, these two parameters can be used to assess the level of caking in powders as they are stored and handled. For many applications, powders change unexpectedly as they move through processing equipment and these changes adversely affect material performance. These changes can be subtle and hard to detect by other means.
ConclusionsIt is found that caking in powders under both static and dynamic conditions directly affect their dynamic flow characteristics and can create instabilities in these characteristics as the materials are subjected to dynamic forces. The dynamic flow characteristics measured include avalanche energy and dynamic density. It is also found that the level of caking in a powder can be assessed by measuring changes in its dynamic flow characteristics before and after exposure to static and dynamic conditions. The unconfined yield strength is not a strong predictor of how a powder will behave in dynamic flow situations.
ReferencesJENIKE, Gravity Flow of Bulk Solids (Bulletin No. 108), Utah Engineering Experiment Station, University of Utah, Salt Lake City-Utah, 1961.
RÖCK AND SCHWEDES (2005), Investigations on the caking behavior of bulk solids—macroscale experiments, in Powder Technology, Volume 157, Issues1-3, 29 September 2005, Pages 121-127
FITZPATRICK, BARRINGER, IQBAL,(2004) Flow property measurement of food powders and sensitivity of Jenike’s hopper design methodology to the measured values, J Food Eng, 61 399–405.